-By Ankita Dutta.
To produce smart fabrics that can detect their environment and react to it, a group of global researchers combined electronic, optoelectronic, sensor, and energy fibre components. The study team, led by the University of Cambridge, developed a means to create the materials using the looming techniques now used to make clothing, making the production of the smart fabrics significantly less expensive.
The authors of the paper claim that their investigation shows how smart textiles could be employed as less expensive substitutes in the building, automotive, electronics, fashion, and apparel sectors.
Despite recent advancements, the functionality, dimensions, and shapes of smart textiles have been severely constrained up to this point because of pricy manufacturing procedures that cost “billions of pounds” to implement.
Using specialised manual laboratory equipment, the global research team has previously shown that enormous woven displays could be created. In microelectronic fabrication facilities, additional smart textiles can also be produced, although these are very expensive and generate a lot of waste.
The research team discovered that flexible screens and smart fabrics may be made at a significantly lower cost by weaving electrical, optoelectronic (light detection and control), sensor, and energy fibre elements on the same commercial looms that are currently used to construct traditional textiles.
The study, which originally appeared in the Journal Science Advances, discovered that if smart textile fibres were coated with polymers that could survive stretching, they could be employed in traditional production procedures. Using this hypothesis, the researchers created a 46-inch woven demonstration display, demonstrating that smart textiles may be generated using automated techniques with no restrictions on the size or form of the fabric.
Multiple types of fibre devices, such as energy storage devices, light-emitting diodes, and transistors, were created and blended with traditional fibres, either synthetic or natural, to create smart textiles by automated weaving. These fibre devices were linked together using an automated laser welding technique and electrically conductive adhesive. All these procedures were optimised to minimise damage to electrical components, resulting in smart fabrics that are strong enough to endure the strain of a commercial weaving machine.
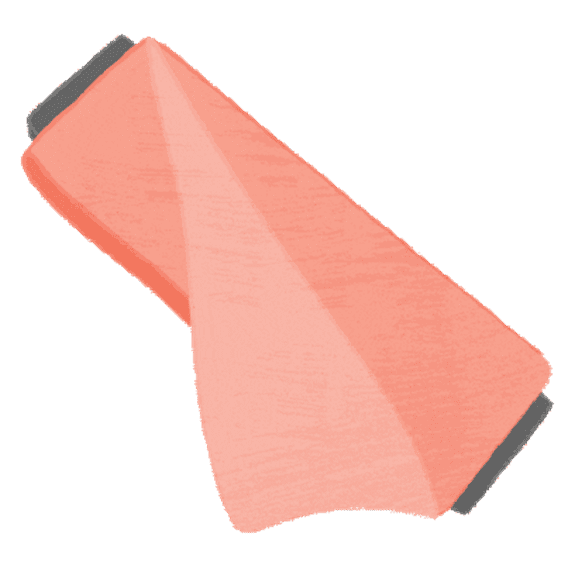
Dr. Sanghyo Lee, the study’s initial author, discussed how the team’s results could aid in the development of future smart fabrics. “We could make these textiles in specialised microelectronics facilities, however, these demand billions of pounds in investment,” said Lee of the Department of Engineering at the University of Cambridge.
“Smart textiles have also been restricted by their absence of practicality,” stated Department of Engineering co-author Dr. Luigi Occhipinti. “Think of the stretching, bending, and folding that typical fabrics undergo, and it’s been challenging to integrate that same sturdiness into smart textiles.”
The study team collaborated with textile manufacturers to create test swatches of smart textiles of roughly 50cm by 50cm, which they claim may be scaled up to greater sizes and produced in higher volumes.
Ankita Dutta.